球墨铸铁型材因其良好的力学性能、铸造性能及较低的生产成本,得到越来越广泛的应用,球墨铸铁型材占铸总产量比例逐年升高。但由于球墨铸铁型材凝固过程中产生的石墨化膨胀,对铸铁型材有压力作用,冒口的大小需要综合考虑多种因素而计算复杂;并且球墨铸铁型材结构越来越复杂,冒口定位效率低,因此复杂球墨铸铁型材的冒口设计比较困难,从而导致目前的球墨铸铁型材铸造工艺CAD系统比较少且功能不够完善,其中的冒口设计模块定位慢,不能针对不同铸型强度进行相应冒口设计。对出现在铸铁型材内部的夹杂缺陷,进行了地研究分析,明确了夹杂物的分布规律、元素组成、来源及形成原因,并就如何控制该缺陷的产生给出了相关的建议。对大断面型材表面出现的疤皮缺陷,分析了形成原因,讨论了影响其形成的因素,并提出了能有效疤皮缺陷的措施。优化设计后得到的铸铁型材新生产线,能够满足 尺寸为400mm的铸铁型材的生产,且生产铸铁型材的工序简化,各设备的结构组成更为简单合理.铸铁型材中的夹杂物主要聚集分布在其中心线上方约3/4半径处,其中大尺寸的夹杂物主要来源于球化和孕育处理,因此解决铸铁型材内部夹杂问题的关键是控制球化和孕育处理的相关参数.对于铸铁型材表面存在的疤皮缺陷,生产实践证明,采取提高铁水温度、保证铁水纯净度、适当提高拉拔速度、该冒口设计方法包含冒口定位和冒口计算,在应用距离场计算几何热节技术的基础上建立基于几何热节的复杂球墨铸铁型材冒口定位方法;同时以收缩模数法为基础,引入铸型强度因素,设计数值模拟方案,借助华铸CAE平台进行模拟,分析归纳数据建立考虑铸型强度的球墨铸铁型材冒口计算方法。
亿锦天泽钢铁有限公司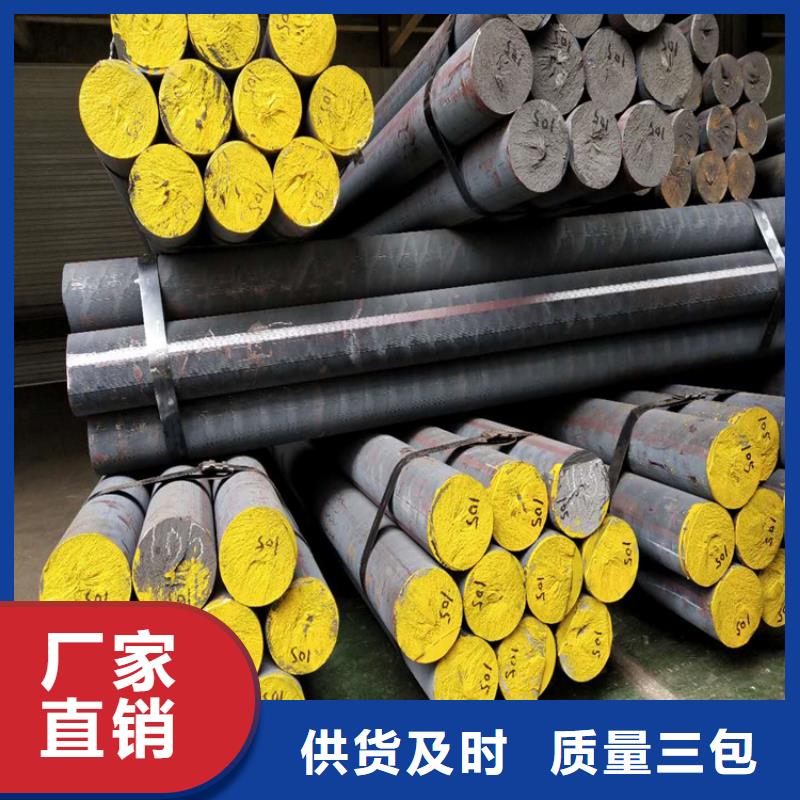
铸铁型材是可以焊接材料。一般只用来焊补铸铁件的铸造缺陷以及局部破坏的铸铁件。铸铁的焊补一般 采用气焊或焊条电弧焊。采用水平连铸和封闭结晶器的工艺使型材表面质量好,尺寸精度高,无夹砂,夹渣,气孔,缩孔等铸造缺陷,加工成品率高于砂铸件。 机械加工性能良好,与砂铸件对比同材质型材切削性能好,铸铁型材切削抗力大于砂铸铸铁件而小于钢件,表面光洁度好,与砂铸铸铁件,钢件对比,铸铁型材在不同速度下切削,表面光洁度相对波动小,不仅在低速(<50m/min)?切削,而且在高速?(>200m/min)?切削时,均能保证表面粗糙度不大于20。 对鼓肚缺陷,在铸铁型材的水平连铸过程中采用反弧度法工艺,即通过新型的石墨套与引锭装置来实现的,通过实施反弧度法工艺,铸铁型材的鼓肚现象得到有效。但由于在率次实验过程中,刚开始生产铸铁型材时的拉拔速度比较慢、拉拔周期较长,使铸铁型材在结晶器的停留时间过长,导致在扁平方向上铸铁型材顶部略微向下凹,当拉拔参数调整合适时,下凹及鼓肚现象基本消失。 体时所需的原子扩散量较小,渗碳体的晶核易形成,所以自合金液体或奥氏体中析出的是渗碳体而不是石墨。 球墨铸铁铸造厂、铸铁型材生产商、球墨铸铁棒,那么影响铸态球铁生产稳定性的因素很多,要稳定地生产球墨铸铁,必须在生产中把握好以下几点:稳定的化学成分和铁液温度,准确的铁液量,合适的球化和孕育处理方法,以及可靠的炉前控制。首先,是在设备上的选择。
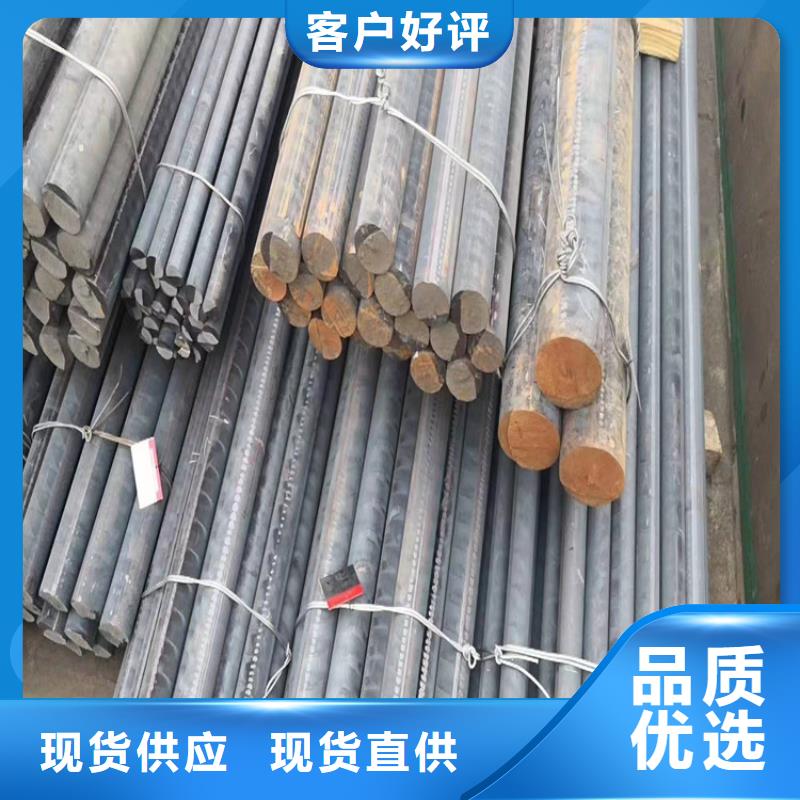
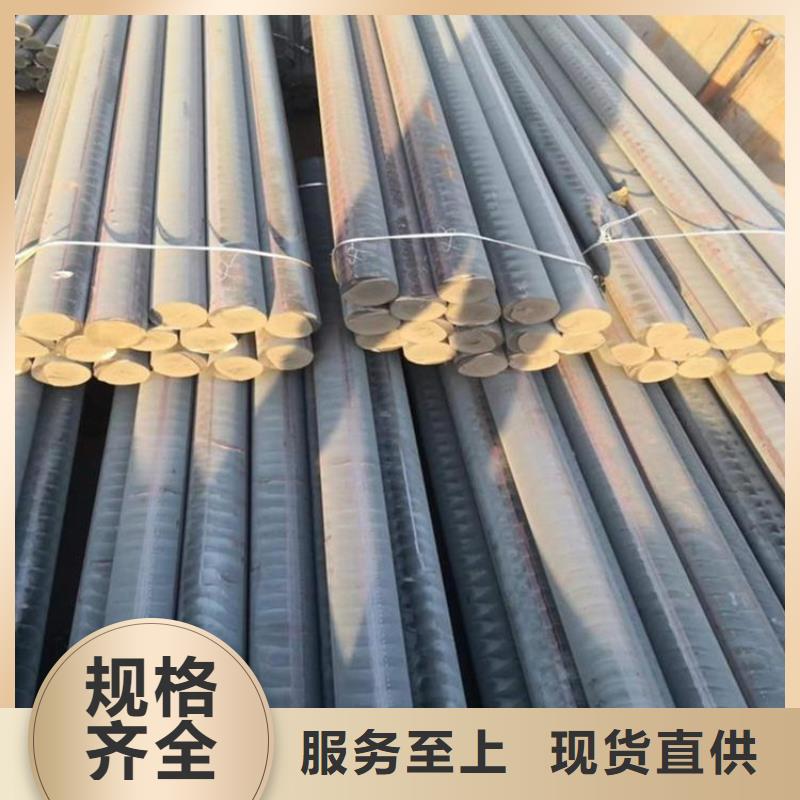